Specifications
The system of closed-joint façades is an innovative solution that makes it possible to cover a building with a ventilated façade in Mirage® porcelain stoneware, leading to numerous benefits from the point of view of the final appearance, energy needs and convenience.
It is possible to achieve a minimum joint size with the closed-joint system, sealing the joints using special aluminium sections, resulting in a very attractive, designer-look.
This helps to create macro-ventilation in the façade’s air gap, unlike façades with open joints, and makes it impossible for insects to get into the air gap.
Specific description of the system
The aluminium substructure is pre-assembled onto the porcelain stoneware slabs using a special interlocking system and a special alignment guide. This offers several benefits during installation and for the performance of the finished façade.
The pre-assembled substructure makes it easier to control the project materials during preparation, and to adapt the covering slabs during the work. This makes it a very flexible solution and results in more freedom when designing the façade.
The processing of the slabs and the assembly of the slabs onto the main aluminium substructure is completed at the factory, allowing for detailed and accurate preparation of the material needed for the installation on site.
Closed joints
The aluminium substructure has large overlapping areas that act as a guide facilitating the installation, thanks to special processes carried out with work centres, and are also a very practical and high quality feature. The closed joint prevents water ingress in bad weather, unwanted access by insects, and ensures there is no break in the air gap for optimum ventilation.
The industrialisation of the slab production process
The processing of the slabs and the assembly of the slabs onto the main aluminium substructure is completed at the factory using high-precision CNC machinery. Similarly, the structural bond between the metal “frame” and the porcelain stoneware is completed on the production line, safeguarding compliance with the procedures for using resins, and guaranteeing the product’s durability and long life. Despite the industrial nature of the pre-assembly of the slab and substructure, there is no impact on the flexibility of the installation because two sides of each slab can still be cut on site.
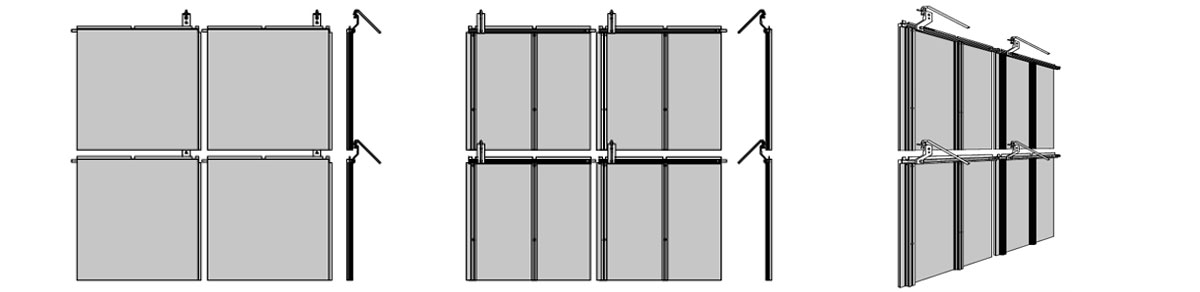
Managing the joints
The joints must be handled systematically with a closedjoint system. The designer first decides the ideal sizes for the horizontal and vertical joints. During the industrial production stage, the work centres determine the size of the joints with absolute precision (tolerance 0.05mm): (from 2 to 8 mm.), (jointless version available on request).
During the installation on site, the fitter simply sticks to the predetermined interlocking connections and the joints will automatically be the chosen size.
Managing the various shapes
The substructure is designed and produced on an industrial level, and is subsequently preassembled onto the porcelain stoneware slab.
Models can be created to use various shapes of preassembled slabs that are compatible with one another. This leads to the possibility of assisted modular solutions such as: 30x60 slabs in combination with 60x120 slabs placed vertically or horizontally.
Similarly, panels can be created using different shapes or using the aluminium sections so as to have interlocking connections demanding the assembly of slabs on site in different sizes and with joints that are not aligned. These architectural choices are transferred to the metal substructure during production at the factory and consequently simplifying the actual installation on site.
Fitting the grid system on site
Aligning the joints with the geometrical lines of the openings depends on the drawing measurements matching the actual measurements on site: this is not always possible because of mistakes or minor variations.
With the closed-joint system, adjusting and adapting the slabs on site is a very simple operation because the substructure is designed so that the slabs are basically a grid system without affecting the guided interlocking system and overlapping areas.
Anchoring the slabs
The slabs are anchored mechanically and chemically to the structure. A special, silicone structural adhesive acts as a vibration-damper between the aluminium and the porcelain stoneware, as well as to contributing to the seal of the system. The system is then secured using special mechanical anchoring devices that guarantee a secure seal.
Wall anchoring
This is a certified anchoring system designed specifically for ventilated façades. It provides a brilliant response when applied to any curtain wall support, even those with a low consistency such as hollow bricks. The certified resistance is approximately 230 kg for each anchor point.
Therefore, it is extremely simple for the designer to cater for demands for different resistance ratings. For example, wind stress is known to be more severe at the higher extremities of an elevation being covered and anchoring devices can be added to cater for this, meeting the most stringent requirements for the permissible load.
Ease of installation
The industrialisation of the ventilated façade makes the system easy to install, resulting in improved productivity on site, a more satisfactory final appearance, enhanced functional qualities, and a very competitive price.
Dismantling
There are two reasons and methods of dismantling the system: